Causes of Aircraft Vibrations and Maintenance Tips
October 31, 2019
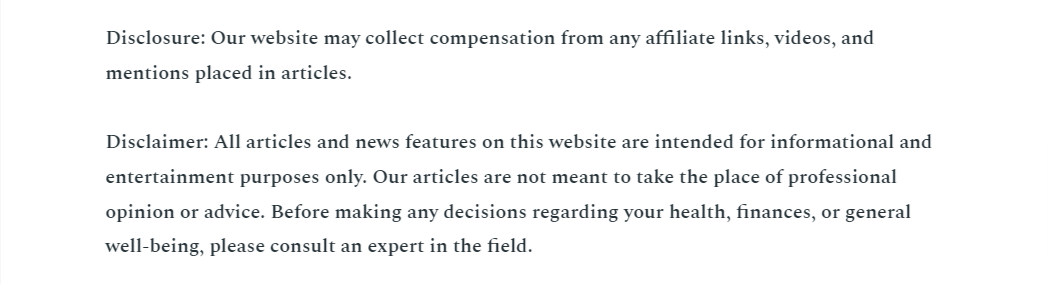
Aircraft maintenance is one of the most important aspects in the aerospace industry. In 2017, the industry employed 131,500 service technicians and mechanics in the U.S. Parts that are not in good shape can lead to the fan, compressor, or turbine cracking. If unattended, the problems can lead to metal fatigue and, worse, an engine failure, which in turn can result in catastrophe.
Aircraft vibration is a common mechanical and technical problem in the aviation industry. In fact, engine vibration is one of the most dreaded problems in aircraft. Analyzing and balancing vibration is a very complicated task. The structural characteristics of each aircraft only exacerbate the problem. Some common vibrations issues in aircraft are engine vibration and bearing vibration. Aircrafts are designed to minimize or completely eliminate vibrations. Vibrations not only pose a danger, but also make the trip uncomfortable.
Causes of Vibration in aircrafts
Aircraft imbalance is a leading cause of engine vibration.
Aerodynamic Imbalance
If the mass distribution of the rotating components is asymmetrical aerodynamic vibration is bound to occur. When the propeller is not installed appropriately, the propeller’s center of gravity will not coincide with the axis.
Fan balance is crucial as it produces force to move the aircraft. A propeller that is poorly installed can lead to aircraft crashes. Testing will determine if the vibration is emanating from worn out parts such as bearing, rotor imbalance, or both. A vibration meter can help to determine if aircraft vibrations are coming from the propeller.
Engine imbalance can be caused by the replacement of fan blades and other rotating parts of the engine. Bird strike, among other impacts, can also cause imbalance. Lastly, corrosion and wear can also cause engine imbalance.
Mass Aircraft Imbalance
Aircraft weight should be distributed proportionally. Otherwise, certain vibration levels will occur. However, the distribution of aircraft weight ought not to be 1000%. A damaged propeller, installation problems, corrosion, and poor maintenance are some causes of mass aircraft imbalance. A vibration meter comes in handy in detecting vibration caused by these factors.
Bearing Vibrations and Fuel Flow
Bearing vibration occurs due to a failure to check the helicopter rotor track and balance. Rotor track balance reduces bearing vibrations. As propeller continues to rotate it makes the bearing weak at the bottom. As a result there is imbalance between the aircraft center of gravity and center of rotation. Maintaining aircraft regularly plays a crucial role in eliminating bearing vibrations. Removing worn out bearing is imperative in bid to avoid intense aircraft vibration.
Fuel flow from the tank to the engine also causes aircraft vibrations. However, fuel flow vibrations are not dangerous.
The severity of aircraft vibration depends on the vibration level. In any case, aircraft are expected to produce some level of vibrations when working. Aircraft vibration in the range of 1.01 to 1.2 IPS is not only rough but very dangerous. If the aircraft emergency landing is not deployed, it could lead to serious problems such as fatal accidents.
Major Aircraft Maintenance Tools
1. Vibration Meters
Vibration meter guarantees aircraft safety when in the air. It measures the vibration level of an aircraft in kilos. A vibration meter shows the maximum vibration that an aircraft can hold. By using a vibration meter, the pilot can determine the vibration magnitude and act according to maintain the integrity and safety of the aircraft.
2. Speed Handle
A speed handle is one of the most advanced and vital tools for aircraft maintained. It enables technicians to remove screw quickly especially in massive engines with colossal numbers of screws.
The best thing to do when the propeller is not in balance is to balance it dynamically. A propeller that is out of balance will cause significant vibrations. A balanced propeller reduces maintenance costs and ensures a safer and smoother ride. Aircraft vibrations increase gradually. Since they are not obvious, it becomes harder for pilot to notice until they are severe. This is where a vibration analyzer comes in handy. It helps to detect and resolve vibration, hence prevent damage.
Aircraft vibrations are quite common occurrences that should be expected. However, it is important to use vibration meter to determine the vibration level and take necessary maintenance measures. Schedule maintenance can do away with some vibrations.