Understanding Different Plastic Molding Processes
December 11, 2019
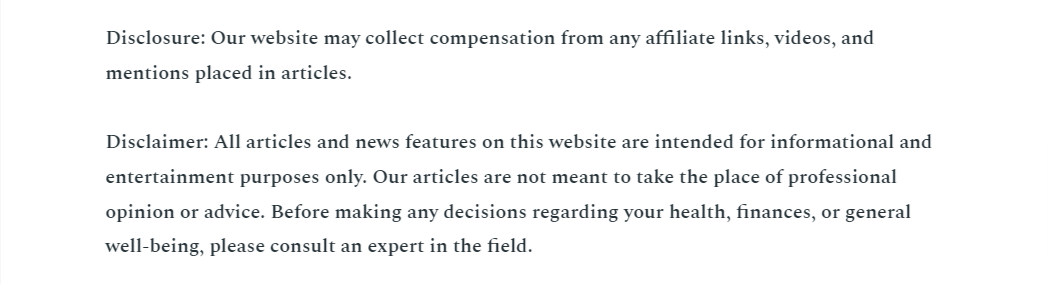
As the world’s third largest plastic producer, the United States is counted on around the world to produce plastics of all kinds. In fact, nearly a million Americans work in plastic manufacturing.
When it comes to plastics manufacturing, there are many processes used including:
- Structural foam molding: A process whereby gas is added to a melted polymer, which is then put into an injection tool via a sprue bushing and nozzle. This process allows lighter, but more durable parts to be manufactured.
- Reaction injection molding: A process where two liquids are mixed and eventually chemically react in a mold. This process allows manufacturers to shape details into their plastics, such as intricate shapes since the plastic is pressed harder inside the mold compared to other processes. RIM also allows fillers to be added to molds, which can increase the density and strength of plastics. It is also a very efficient process since many parts can be created from just one mold.
- Polyurethane injection molding (plastic injection molding): This process sees the injection of different kinds of molten materials into molds through a sprue bushing and nozzle. Die-casting is one such process that is done this way. Materials are placed into mold cavities and harden as they cool, ultimately creating plastic molds.
When it comes to injection molding, there are a lot of important parts such as sprue bushings, machine nozzles, dual stage filters and valve gate systems.
A dual stage filter protects the hot runner system of a molding machine, which helps avoid clogging and backups potentially caused by metal that is used in injection molding. Dual stage filters are typically mounted on a molding apparatus between the molding nozzle and extruder barrel. The design of a dual stage filter allows for two separate melting pathways during the molding process. One path on a dual stage filter is for injection, where a melted material is filtered and another path during the point where the mold is decompressed.
Each type of plastic molding has several advantages. By knowing the differences and benefits of each of them, a plastics manufacturer can save a lot of time and money while producing high-quality parts consistently and with the greatest level of efficiency.